How Do You Know if You Have Aluminum Wiring?
Understanding whether your home has aluminum wiring is crucial for maintaining electrical safety. Older homes, particularly those built between 1965 and 1972, may contain aluminum wiring—a material that, if not properly maintained, can pose significant risks. That’s where Aluminum Wire Repair, Inc. comes in! Our team based in Longmont, CO, and serving the Colorado Front Range offers reliable aluminum wiring repairs for residential and commercial properties. Whether you’re in the process of buying property or have noticed the signs of aluminum wiring, our expert electricians can help!
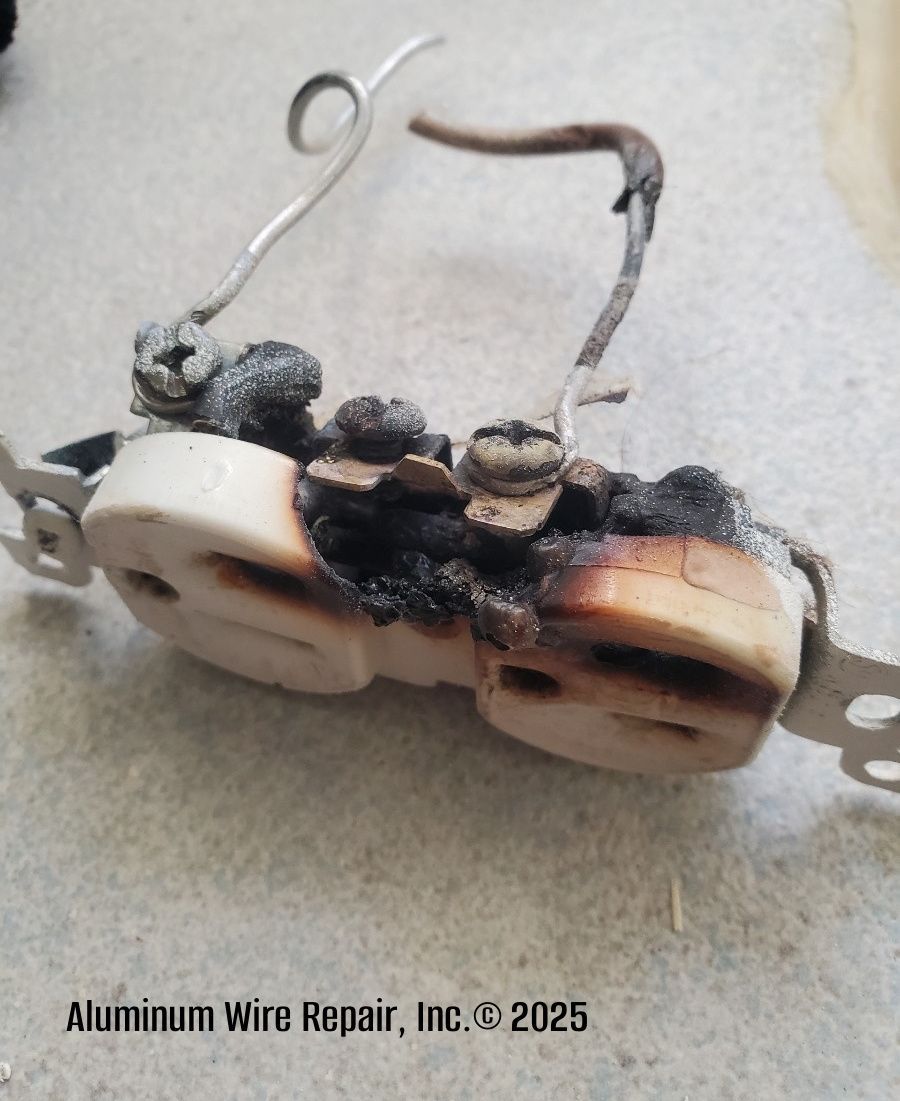
Common Signs of Aluminum Wiring in Your Home
Identifying aluminum wiring can help you address potential safety concerns early. Look for these common indicators:
Deteriorated Connections:
Flickering Lights or warm-to-touch face plates are signs of deteriorated connections
Unique Labeling:
There may be indications of aluminum wiring in the electrical panels or wiring jackets in exposed areas - such as a furnace room.
Inconsistent Voltage:
Fluctuations in voltage or frequent circuit breaker trips may also be a sign of aluminum wiring issues.
Historical Use of Aluminum Wiring
Many homes built from 1965 to 1973 utilized aluminum wiring due to its cost-effectiveness at the time. While it provided an affordable alternative to copper, the long-term reliability of aluminum wiring has proven to be problematic without proper maintenance and updates.
Dangers of Aluminum Wiring
Aluminum wiring can pose several hazards if not correctly managed. Key risks include:
Increased Fire Risk:
Aluminum wiring can overheat, leading to potential electrical fires.
Corrosion and Oxidation:
Oxidation can degrade connections, increasing the likelihood of electrical faults.
Loose Connections:
The natural expansion and contraction of aluminum can lead to loosening over time, compromising the integrity of electrical circuits.
Electrical Shock:
Deteriorated wiring may not provide a safe grounding path, elevating the risk of shock.
If you suspect your home may have aluminum wiring, it’s important to have it inspected by a qualified professional. Addressing these concerns early can help safeguard your property and the well-being of your family.
Understanding the importance of updating dated aluminum wiring in your home has never been easier. Let the expert team at Aluminum Wire Repair, Inc. help you!